IT Security Company Case Study (ITAD)
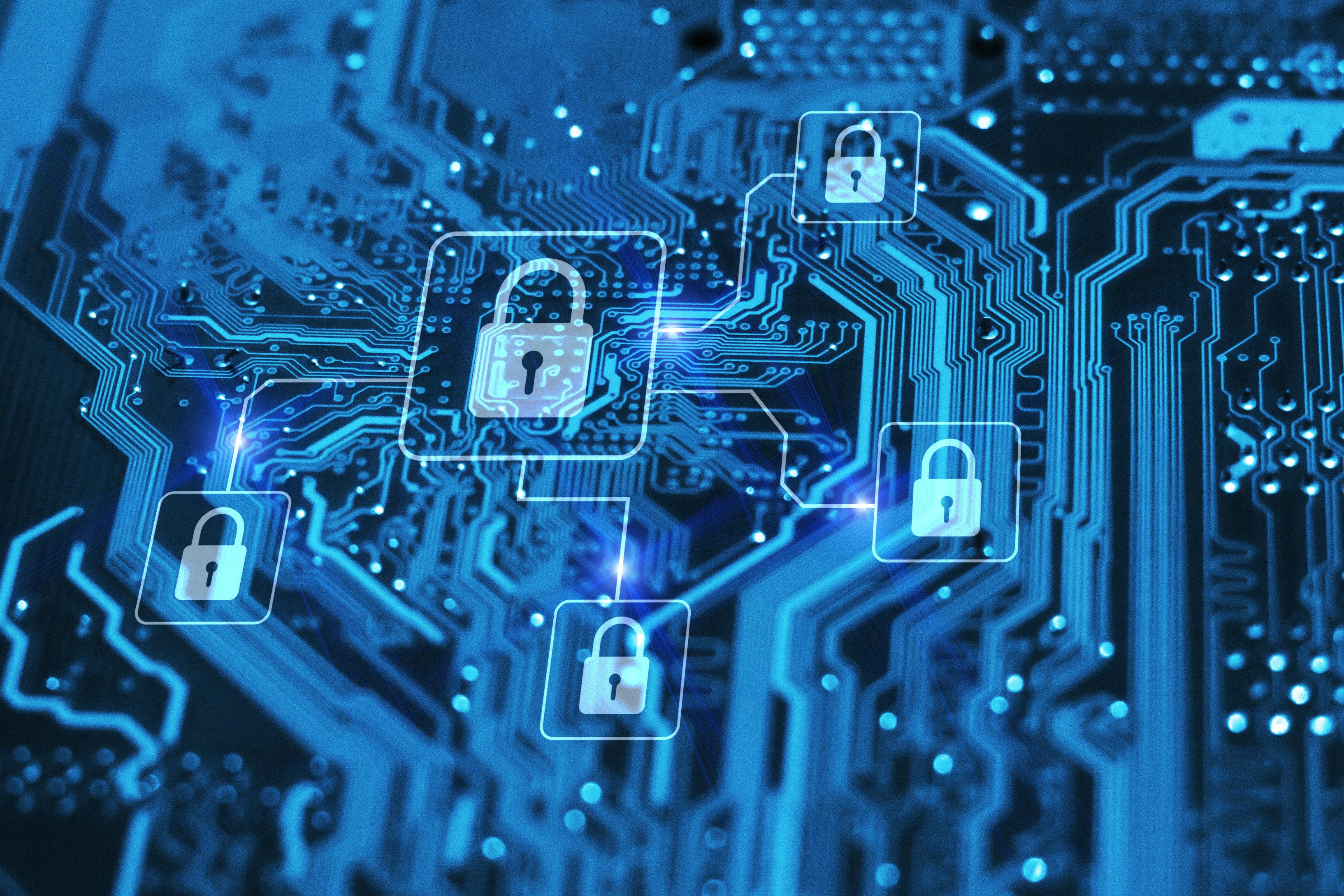
Summary
EXTEND, PivIT’s professional services offering to work with an IT security company migrating its nonproduction environment into the cloud. EXTEND first staged a phone call with the IT security team, Project Manager, and Director of IT to discuss the initial requirements, locations, and timelines. It was determined that EXTEND would first stage a team of engineers to identify physical assets at their Hamburg, Germany, location to better understand the environment.
- Devices: 859
- Media Devices (HDD, SSD, Tape, Flash Card): 3,022
- Equipment ROI: $88,000
- Equipment License ROI: $130,000
- Building Lease Termination: $66,000/month
Customer's Needs
The customer needed to migrate its non-production environment into the cloud. They required additional engineers to conduct an equipment audit, which could determine the necessary equipment to be decommissioned. The client also wanted to resell nonfaulty equipment using PivIT’s Hardware Buy Back Program. Lastly, they needed the equipment disposed of securely.
PivIT's Solution With EXTEND
Step 1: Audit
An initial equipment audit report was conducted and discussed with the customer, including rack/floor placement, rack elevation, make, model, serial number, and status. The report allowed the customer and PivIT to create a decommissioning schedule.
Some of the customer’s legacy equipment was repurposed within the organization and relocated to their primary data center in Frankfurt, Germany. The remaining list of assets was evaluated against the market value, and a high-level offer was provided for the purchase of this gear and the logistics costs to remove it from the site.
Step 2: Planning and Execution
Project planning, both onsite or via conference call, took place bi-weekly until a project plan was formed and the offer was accepted to remove the final equipment list from the site.
EXTEND staged a team of engineers onsite to de-rack, de-cable, remove sensitive media, and transport all equipment indicated on the audit list to a staging area.
All sensitive media devices were degaussed within their current locations before being transported to the onsite destruction team for serial number, make, and model auditing. These media devices were finally shredded to 3.5mm in size in witness of EXTEND personnel. A complete audit list was provided to the customer via USB drive and certificate of destruction.
Step 3: Finishing Touches
The remaining equipment was packed and palletized at the loading dock for transportation to a secured and monitored facility, where each device with an initial noted market value was tested for physical and functional performance in a lab environment.
The equipment was resold through EXTEND’s channel, and the remaining equipment was recycled according to local law and regulation. Within 30 days of the equipment arriving at the facility, a check and a certificate of recycling were issued to the client.