Busting Myths About Third-Party Maintenance With Data
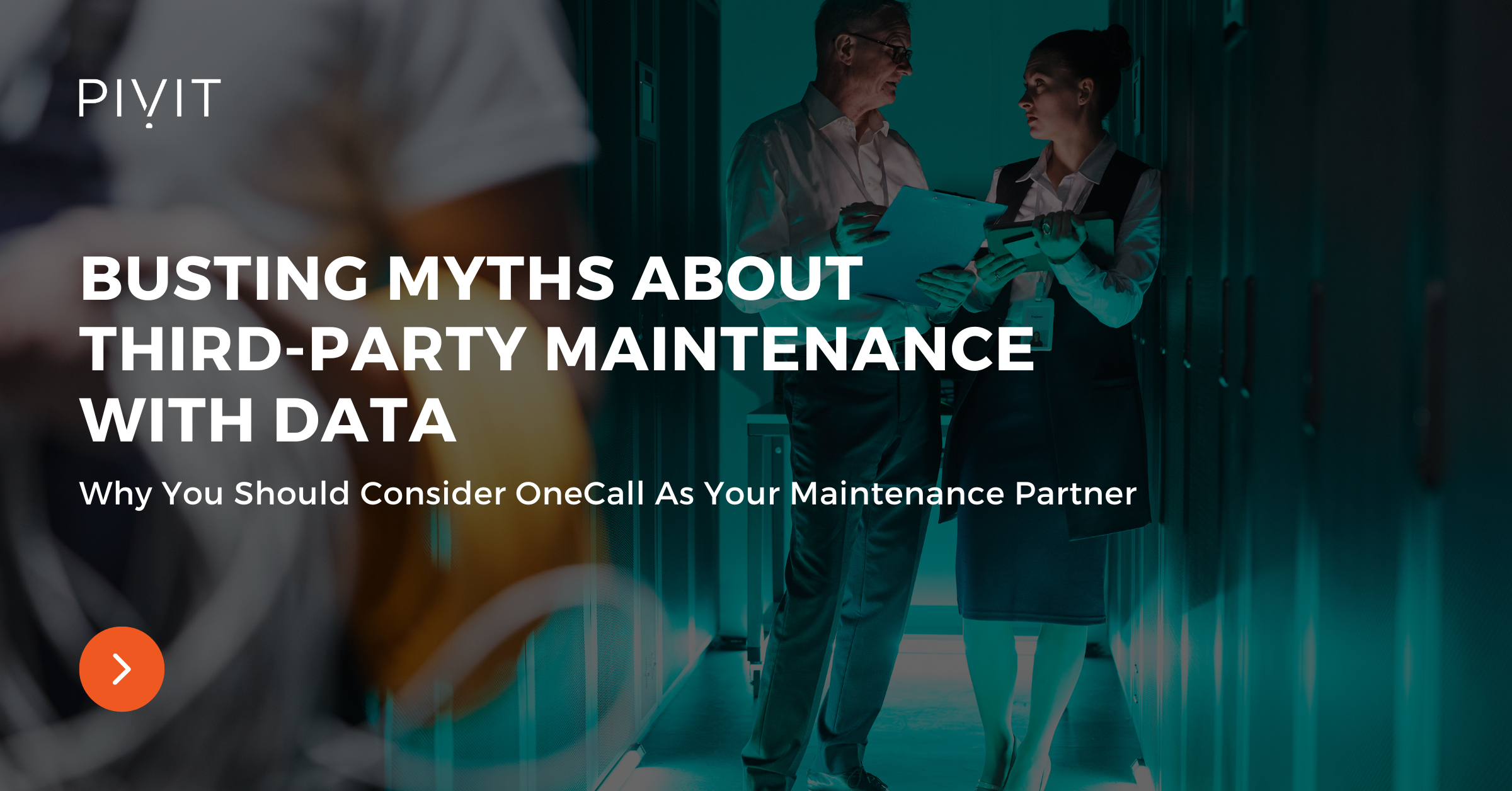
Third-party maintenance (TPM) involves support, repair, and other maintenance services provided by an external party other than the original equipment manufacturer (OEM). TPM is gradually becoming the preferred choice for IT enterprises looking for cost savings and convenience. But many myths about it remain, keeping companies on the fence.
TPM offers many benefits, particularly for maintaining legacy equipment, which OEMs often don’t cover. It’s a saturated market with many players; no two TPM providers may be the same. Yet, it’s worth it to tap into its many advantages for your business.
This article aims to bust the myths and misconceptions around TPM and present the truth with proof.
5 Myths About Third-Party Maintenance (TPM)
Enterprises concerned about TPM may want to distinguish between myths and facts. Here are the most common myths about TPM explained and expunged:
Myth 1: TPM Is Expensive
The most common TPM myth is that it costs more than OEM. Another rendition of this myth is that it's simply too costly to maintain legacy equipment and just better to refresh.
The truth is that OEM support is typically way more expensive than TPM, especially as the equipment ages. Most OEMs only extend support till the end of service life (EOSL) milestone. However, those who offer maintenance beyond that point do so at exorbitantly high premiums. TPM support is much more budget-friendly, especially for legacy equipment that no longer has OEM maintenance.
Depending on the TPM service you choose, the quality and the service level agreements (SLAs) may be comparable to OEMs but at a much lower price point.
OEMs typically increase maintenance coverage prices as devices age, pushing customers to buy new ones. Even if the equipment works fine, customers may buy new ones only to avoid the hefty costs of maintaining old equipment with an OEM.
Consider this: Enterprises can save 40% to 60% on maintenance by choosing a third party over OEMs. Most PivIT clients using the OneCall platform have, on average, saved 60% on maintenance.
Myth 2: TPM Lacks the Expertise
Another myth about TPM support is that it’s not as good as OEM support. Since OEMs are the companies designing and manufacturing equipment, they are the best to maintain it. By that logic, OEMs should have better expertise and deliver higher quality. But did you know that many OEMs contract third parties to provide maintenance?
In many regions, OEMs may not have their own engineers present, so they outsource such services to local companies. While they do maintain strict standards, this whole arrangement goes to show that for quality service, it’s not essential that technicians directly come from the brand.
Simply put, a knowledgeable engineer with hands-on experience with a particular brand or series can deliver reliable maintenance service. Even when the device needs repairs, these engineers can fix them effortlessly.
In general, TPM providers don’t necessarily lack technical expertise. The overall quality may differ from one provider to another. But as far as expertise goes, any TPM provider can offer a similar level of support as OEMs with the help of experienced engineers.
At PivIT, our hardware engineers have a collective experience expanding over decades. More importantly, unlike OEM engineers and technicians, PivIT’s experts are not limited by a single vendor. They are proficient in maintaining and fixing equipment regardless of the brand, making them suitable for today’s multi-vendor environments.
Myth 3: TPM Support Isn’t Dependable
Many enterprises refrain from going with a third party for maintenance and support because they believe they can’t rely on them. As OEMs must uphold their brand name and reputation, they would likely provide a more reliable service.
Such assumptions fail to consider that TPM providers often have similar SLAs as the OEM, sometimes even better. Moreover, enterprises can get more customized contracts, which is something OEMs don’t provide.
When contracting with big vendors for maintenance, it’s typically them dictating the terms. TPM providers are not locked by a single vendor, so they can provide more contract flexibility.
Moreover, SLAs may be too long in certain regions where an OEM may not have a strong presence. You can’t wait for a device to be fixed or replaced for days.
TPM providers use a network of service providers to ensure that support is issued in the agreed-upon timeline.
With PivIT’s OneCall offering, customers can get SLAs as short as four hours! Even OEMs cannot guarantee such short SLAs.
Myth 4: TPM Is Difficult to Manage With OEM Contracts
Another concern for large enterprises considering TPM support is that it will only increase complexity. In other words, they believe that having OEM and TPM contracts will complicate management.
This is a possibility but can be handled with the right tools. A hybrid maintenance approach can be highly cost-effective if executed well.
With OneCall’s proprietary OneHub console, enterprises can manage OEM contracts and agreements with OneCall. In other words, this portal brings all maintenance contracts in one place, whether with the manufacturer or a third party.
With the help of OneCall and OneHub, a global beverage company managed to save $1 million in annual maintenance costs. As a multinational company with different locations and working with many vendors, their SLAs were highly fragmented. However, by opting for OneCall for some of their maintenance needs and moving all contracts to one system, the company removed complications and saved significantly.
Myth 5: EOSL Is the End of Maintenance
This myth has more to do with the hardware lifecycle than maintenance. Many enterprises consider EOSL as the death of the equipment, mainly because OEMs don’t provide support after that. However, the equipment can last longer than its intended EOSL period.
The lifespan of the equipment after the EOSL date depends on various factors, such as its condition. However, it can easily last for another few years with proper maintenance.
For instance, networking equipment may only have OEM support for three to five years. However, it may continue to function for up to 10 years.
OEMs want customers to refresh as soon as equipment reaches EOSL. It’s the customer’s discretion whether they want to update the device or continue with the existing model with the help of TPM.
By extending the life of the equipment and delaying the refresh cycle, TPM providers can save IT enterprises considerable money. So EOSL isn’t the end of the product or its maintenance.
Consider Maintenance With OneCall
OneCall is a comprehensive solution for both short-term and long-term maintenance. Your business is only as good as the infrastructure it’s based on. If the infrastructure isn’t reliable, uptime and availability will suffer, compromising the enterprise’s productivity and reputation.
With OneCall, organizations can save on maintenance, particularly for legacy equipment that has reached EOSL. But that’s not all; OneCall allows customers to continue using OEM support for new equipment and manage all contracts from a singular portal, OneHub.
OneCall, backed by highly skilled engineers, provides support globally with some of the shortest SLAs in the industry.