How to Resolve Logistics Challenges With Network Equipment Procurement
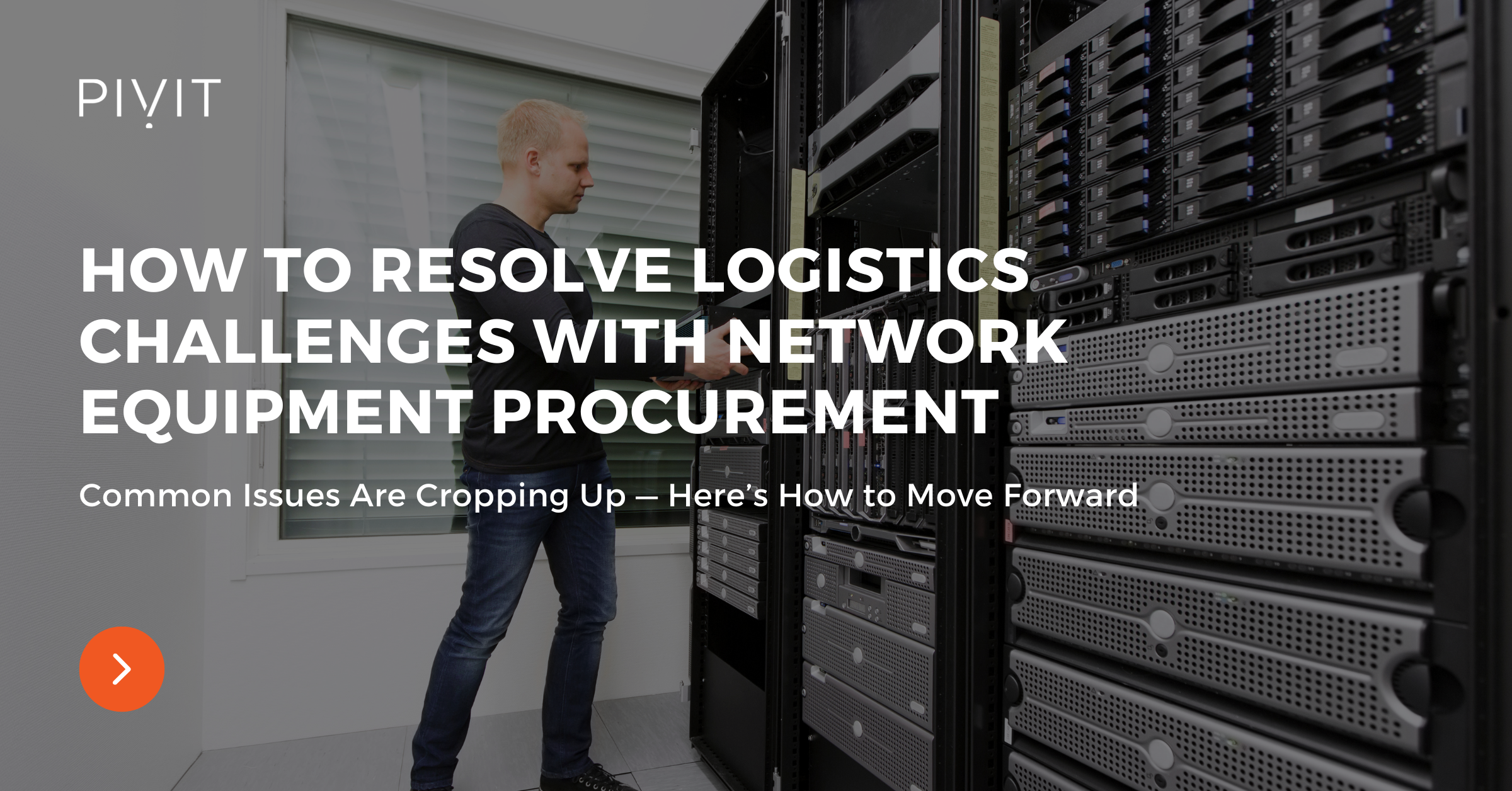
IT sourcing and procurement have lately been marred with many challenges related mainly to logistics. Thanks to the global supply chain crisis that began after the COVID-19 pandemic, supply for critical hardware components has been slow.
But that’s just the tip of the iceberg, as the logistics of sourcing network equipment in time is complex in the good times, let alone times of crisis.
Enterprises that heavily rely on network equipment (data centers or telecommunication) often need to procure new gear. But doing so can be difficult because of logistical hurdles that are sometimes beyond their control.
In this article, we will discuss the following:
- Typical logistics problems that result in long lead times.
- Delays in shipment.
- Downright unavailability of gear in certain regions.
- Suggestions on how to navigate these challenges with the help of PivIT.
Not the article you were looking for today? Try out these articles:
- 3 Top Benefits of Efficient IT Asset Recovery and ITAD With PivIT
- Which to Choose? Short-Term vs. Long-Term Maintenance of IT Assets
- Top 3 Ways to Utilize Professional Services for Your IT Team in 2023
5 Common Logistics Challenges With Hardware Procurement
The supply chain industry went into a crisis in 2020 that has yet to end. Though the pandemic is often blamed, the crisis was a long time coming.
The tech hardware industry has significant issues with its supply chain and logistics.
Here are the most common logistical problems companies face when procuring IT network equipment:
Supply Delays
The most common problem rampant right now is simply a supply-side issue. There’s just not that much equipment to go around. But this problem isn’t new, as IT businesses have had to endure supply issues for too long (pre-pandemic, the lead times would be up to six weeks, and now they are over 200 days).
This problem is more common with smaller, high-utility network devices. Supply issues are often linked with components that make up the hardware. If a critical part faces delays, production is delayed, and subsequently, the delivery of the product.
The unfortunate reality is that supply delays are out of the hand of the business ordering the equipment. Companies are left with either waiting for the new gear or sticking with the old one for the time being.
Trade Embargoes
Trade embargoes result in bans on the import/export of certain things, which may also include hardware. For enterprises operating in a region with trade bans from a country where the equipment is present, procuring the hardware becomes impossible.
Again, this is something beyond their control as it’s the governments that put embargoes. However, the impact is pretty significant on the logistics of critical infrastructure and, by extension, the business.
Interestingly, certain regions may have geopolitical hurdles despite having no trade embargoes. While the situation varies from country to country, the common reasons behind logistics taking longer to deliver equipment in certain countries include higher tariffs, lengthy customs checks, remote journeys, or political rivalries.
Third-Party Shipping
Even if you can procure equipment from a vendor in time, another party may cause delays. As OEMs and suppliers often use shipping companies to send network and other IT equipment to different destinations, delays from their partners can also cause delays in your projects.
There can be various reasons behind delays from logistics companies, including personnel shortages like delivery drivers or natural disasters like hurricanes. The cost of such delays is paid by the companies procuring the equipment as their projects and upgrades move further.
Rising Costs
The cost to ship equipment to where you need it is constantly rising, now more than ever, on the back of high fuel prices. In 2021, the US business logistics costs amounted to an unprecedented $1.85 trillion.
The shipping may cost significantly more if you need equipment on short notice and need it delivered the next business day. As a result, procuring hardware is becoming increasingly expensive, which impacts medium and smaller enterprises as higher shipping costs impact their IT budget. The money that previously purchased more equipment or was spent on other business expenditures now goes to shipping.
This rising cost of logistics of hardware procurement may also cause businesses to delay or cancel upgrades altogether. That, in turn, seriously hampers their ability to compete in the market as their competitors embrace newer hardware with better performance.
Lack of Support
Another hurdle you may face when procuring hardware is subpar support from vendors or shipping companies. If your equipment delivery is delayed, it may be hard to track it down should you decide to take matters into your hand.
Quality customer support is an integral component of this trade. While not all OEMs or third-party suppliers have lousy customer support, tasks like tracking your shipment or claiming refunds can become a nightmare if you do business with one that does.
How to Mitigate Logistics Hurdles When Sourcing Hardware
Logistics issues can be challenging for IT companies to mitigate and resolve as shipping is not in their domain. The OEM or suppliers are the ones handling the shipment. So what can you do to avoid all of the problems typical with the logistics of network equipment?
Look Beyond OEMs
Many businesses work directly with OEMs to procure equipment. Besides the usual problems like out-of-stock models, OEMs may not necessarily have consistent delivery times, especially in regions where they don’t operate.
Relying on OEMs exclusively, especially if you’re facing constant shipment delays, is terrible for business. Instead, you need to look for third parties, such as value-added resellers (VARs), to procure equipment faster.
Work With VARs With Global Distribution
When choosing suppliers, go with the one that has a globally distributed inventory. You can research your top picks and finalize one with the most distribution centers or the largest equipment inventory from your preferred OEMs.
A company with a global inventory and distribution channels would be better able to navigate the global supply chain. They could reduce the shipment time as equipment may come from somewhere nearer to your facility.
Compare Prices and Shipment Times
As hardware itself gets more expensive and so does shipping, naturally, you want to get the best prices. Discounts on large orders can go a long way in reducing your IT spending.
Therefore, shopping around and comparing prices and delivery times is best. Both are important considerations because a cheaper option arriving late isn’t all that beneficial. So ideally, you want the lowest price and fastest service level agreements (SLAs).
Try PivIT: The Answer to All Your Hardware Procurement Problems!
PivIT can address the standard logistics issues with hardware procurement thanks to its global outreach and multi-channel sourcing from major OEMs. It isn’t your typical VAR, as the inventory specialists at PivIT work with OEMs and suppliers, having years of expertise in negotiation and networking.
More importantly, PivIT has two attributes that most VARs and even some OEMs don’t offer. First, it has an in-stock inventory of hundreds of thousands of pieces of equipment, including new and refurbished ones. Second, it offers guaranteed delivery according to the agreed-upon SLAs.
Even if you require network equipment that PivIT doesn’t have in stock, it can arrange it for you, working with OEMs directly. And sometimes, you can get prices lower than OEMs and other VARs.
If you’re tired of the hassle of procuring hardware only to have it delivered late, let the professionals at PivIT handle the process. That way, you can receive your equipment on time and focus on improving your infrastructure and growing your business.